|
Production dates and timely deliveries to customers depend on whether we have enough of the necessary items in stock at the right time. Every company that has suffered losses due to downtime or contractual penalties due to supply shortages knows how important it is to diversify suppliers and their reliability. Therefore, companies use the services of several different suppliers for a given product range. Thanks to this, they can count on ensuring continuity of supplies. To optimize purchases and obtain an overview of which products should be ordered and in what quantity, ERP systems offer the possibility of creating the so-called automatic order proposal.
In practice, this functionality allows you to automatically create orders for customers, taking into account inventory in the warehouse. When creating orders, we can, of course, freely change the proposals generated by the system, choosing, for example, deliveries from the cheapest or web designs and development service fastest suppliers, as well as ordering minimal quantities but optimized in terms of logistics. The system also combines many orders of the same article to one supplier or orders of different articles from the same supplier into one order, thanks to which the number of documents processed is smaller.
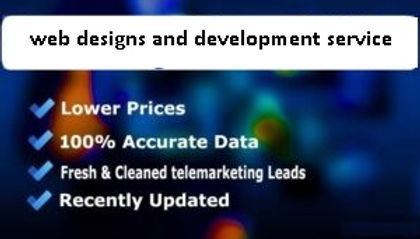
Automatic orders can be created for a selected article or a whole group of articles, e.g. when we want to purchase only a given product range, or for a given supplier, when we order articles from a specific supplier and at the same time want to replenish the minimum stock levels with his articles. There are, of course, many possibilities for optimizing deliveries and you can create individualized filters for your own use. Those described above are only the most important ones, but they greatly facilitate the work in the purchasing department and ensure continuity of supplies in the company. text Automatic price calculation and change Changes in the prices of raw materials from suppliers result in an increase in the prices of manufactured items.
|
|